Foam Moulding: The Innovation Behind Polyurethane Foam Applications
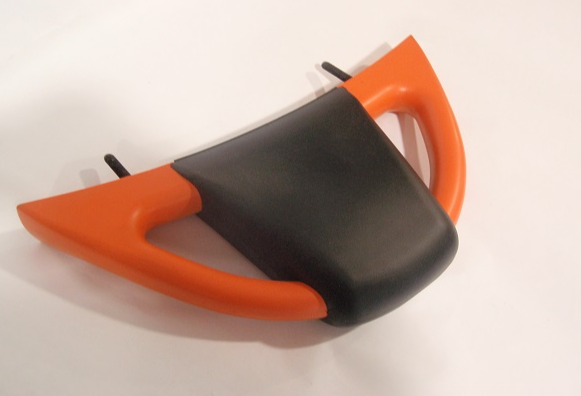
Introduction to Foam Moulding
Foam moulding, particularly polyurethane foam moulding, is a specialized process used to create high-quality, durable, and versatile foam products. This method involves combining materials to produce a foam with a protective outer skin, making it ideal for applications requiring both softness and durability.
One of the most prominent manufacturers in this field is Acoustafoam, a company with over 36 years of expertise in polyurethane moulding technology. Their innovative techniques allow them to produce foam products tailored to various industries, from automotive and furniture to marine and construction.
In this article, we will explore the benefits, applications, and production process of polyurethane foam moulding, highlighting why this technology is crucial for modern industries.
What Is Polyurethane Foam Moulding?
Polyurethane foam moulding, also known as integral skin moulding or self-skin moulding, is a process that creates a foam product with a tough, flexible, and tear-resistant outer layer. The unique self-skinned surface forms during the moulding process, providing an extra layer of protection against wear and tear, scratches, and impact damage.
This type of foam is highly customizable, with variations in density and hardness ranging from 30 to 90 Shore A, depending on the application. Additionally, the surface can be chemically textured to resemble materials like leather, offering an aesthetic and functional advantage.
The Process of Polyurethane Foam Moulding
The foam moulding process involves several key steps to ensure precision and quality. Here’s how it works:
1. Material Mixing and Dispensing
Two liquid components are mixed, triggering a chemical reaction that expands into a foam when dispensed into a mould.
2. Moulding and Curing
The material is allowed to expand and cure inside the mould, forming the desired shape. The self-skinning feature naturally develops, creating a protective outer layer.
3. Trimming and Finishing
Once cured, the product is removed from the mould and undergoes trimming to eliminate excess material, ensuring a clean and polished final product.
4. Quality Control and Storage
Before dispatch, the foam components undergo rigorous testing for density, hardness, fire resistance, UV stability, and structural integrity.
This meticulous process guarantees that polyurethane foam moulded products meet high industry standards and perform effectively in various applications.
Applications of Foam Moulding
Polyurethane foam moulding is widely used across multiple industries due to its versatility and durability. Some of the common applications include:
1. Automotive Industry
- Grab handles, armrests, and headrests for enhanced comfort.
- Steering wheels and gear knobs for improved grip and durability.
2. Furniture Manufacturing
- Seating components with cushioned yet firm support.
- Decorative trims for aesthetic and functional appeal.
3. Marine and Aviation
- Seats and headrests designed for durability in harsh environments.
- Safety products with impact-resistant foam technology.
4. Industrial and Construction Equipment
- Protective padding and handles to ensure worker safety.
- Soundproofing foam components for noise reduction in machinery.
5. Gaming and Entertainment Industry
- Gaming chair components for ergonomic support.
- Arcade machine panels for a comfortable user experience.
The ability to customize polyurethane foam moulding makes it an invaluable resource across these industries, offering both functionality and design flexibility.
Benefits of Polyurethane Foam Moulding
1. Durability and Strength
The integral skin adds an extra layer of protection, making the foam resistant to tears, scratches, and abrasion.
2. Customization and Aesthetic Appeal
Polyurethane foam can be moulded into different shapes, densities, and textures, offering a high level of customization. The skin can be textured to look like leather or other materials, enhancing its visual appeal.
3. Lightweight and Flexible
Despite its strength, polyurethane foam remains lightweight, making it easy to handle and transport while maintaining flexibility.
4. Excellent Shock Absorption
The foam structure provides impact resistance, making it ideal for safety products and automotive interiors.
5. UV and Fire Resistance
Many polyurethane moulded products are treated with UV stable coatings to prevent color fading and fire-retardant properties to enhance safety.
6. Cost-Effective Production
With the ability to create high-quality prototypes and mass production efficiently, polyurethane foam moulding is a cost-effective solution for manufacturers.
Polyurethane Foam in Acoustic and Insulation Applications
Beyond structural and cushioning applications, polyurethane foam is also used for soundproofing and insulation. Companies like Acoustafoam specialize in acoustic barriers made from foam, designed to:
- Reduce airborne noise and improve sound insulation.
- Dampen vibrations in machinery and vehicles.
- Act as a thermal barrier in industrial settings.
These acoustic solutions are widely used in automotive, construction, and home appliance industries, demonstrating the versatility of polyurethane foam.
Read also: Understanding Bridging Loans: Guide for First-Time Homebuyers
Conclusion
Polyurethane foam moulding is an essential technology that offers durability, flexibility, and cost-effectiveness for a variety of industries. Whether it’s automotive interiors, furniture, industrial equipment, or acoustic barriers, this foam solution continues to play a vital role in modern manufacturing.
With cutting-edge techniques and decades of expertise, companies like Acoustafoam have mastered the art of producing high-quality polyurethane foam moulded products that meet the demands of various industries.
If you are looking for custom polyurethane foam solutions, exploring foam moulding technology can offer innovative and practical applications tailored to your needs.